Perth Insulation reduces heat flow, cutting energy costs. All insulation reduces conduction (think of the way metal conducts heat), but some types do so more effectively than others.
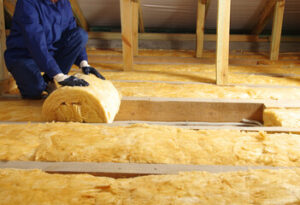
The most common types of insulation are fiberglass, mineral rock wool and cellulose. They are usually installed in walls and attics. Cellulose is available in loose-fill or blown-in form, and also as foam insulation applied wet to wall cavities and around obstructions.
Insulation is material that reduces the flow of heat in and out of a home. It is used to stop heat from escaping in winter and to keep the heat in in summer. Choosing the right insulation for your home can significantly cut energy costs and make it easier to heat or cool your home.
There are several types of insulation including foam, fiberglass and cellulose. Foam insulation works by trapping air between its fibres. This creates an air-sealed barrier that prevents thermal loss and increases energy efficiency. It is also fire resistant.
Fiberglass is made from molten glass spun into fibres and is one of the most common types of insulation. It is available in batts that are installed in wall spaces or rolled into rolls for use in ducts. It is cheap and effective, and is non-flammable. It can be installed in both existing walls and new walls. It has an R-value of between R-2.9 and R-3.8 per inch of thickness.
Polystyrene insulation is similar to MEPS, but it is expanded or extruded. It is also non-flammable and has an R-value of between R-3.9 and R-5.6 per inch of thickness. It is often installed in wall stud cavities or between framing members in new homes. It is also a component of some structural insulated panels (SIPs) and insulated concrete forms (ICFs).
Mineral wool may be made from a range of materials such as natural minerals or industrial byproducts. It is a fire-resistant insulation with an R-value of between R-3.6 and R-3.8 per inch of thickness. It is heavier than most other insulation and can be difficult to work with.
Cellulose insulation is made from recycled paper products and is not only a good insulator, but it is very environmentally friendly. It can be blown into existing walls and open cavities in new construction or as a loose-fill product for blown in cellulose insulation in attic floors. It has an R-value of between 3.1 and R-3.7 per inch of thickness and is non-flammable.
Reflective insulation is a newer type of insulation that uses foil to reflect radiant heat rather than blocking it. It is very effective in hot or cold climates and is often installed in ceilings, but can be used in walls where it will not come into contact with any cladding or services. It is important that reflective insulation is not placed in contact with any other building elements, as this will dramatically decrease its performance.
How Insulation Works
Insulation is designed to stop heat or sound from transferring between areas of the home. It does this in a number of ways depending on the type of insulation you choose, but it mainly restricts energy transfer through conduction, radiation and convection. When you consider how much heat and electricity is wasted in homes that are poorly insulated it makes sense to get your home properly insulated.
The way most insulation works is by trapping millions of tiny air pockets within it. These are an extremely good insulator and can reduce the flow of hot or cold air. Essentially the more air there is trapped within an insulator, the better it will be at stopping convection, radiation and conduction.
There are a number of different types of bulk insulation and the performance of each varies significantly. They all are rated according to their R value, the higher the number the better the insulation. R values are determined by a number of factors including the thickness of the material, thermal conductivity and moisture resistance.
When choosing an insulator it is important to consider not only its R value but also the overall R value of your home construction including any reflective membranes that may be used. This will help ensure that the insulator you choose is suitable for your specific building and climate conditions.
A common misconception is that insulation will insulate your entire home, however this is not the case. You will need to install insulation in all areas where heat can escape or gain entry. This is where insulation can make the biggest difference to your home’s energy efficiency and comfort.
Whether you opt for fiber glass, cellulose, rock wool or any other form of insulation it is essential that it is installed correctly. This will allow it to perform at its best and not lose effectiveness. This will include ensuring that the insulation is placed against and tight to any framing members. It will also need to be installed in accordance with any other relevant Australian standards. The best way to ensure this is to use a professional installer who is familiar with the Australian Standards and building regulations.
How to Install Insulation
Insulation is not only easy to work with, it also saves money in heating and cooling costs and helps buffer noise. However, installing insulation does require some manual labor and power tools. Prior to beginning any project, be sure to turn off the electricity, and always use caution when working with any power tools. Additionally, it’s recommended to wear a mask and eye protection whenever working with spray foam or using hole saws.
When insulating walls, be sure to follow the specific recommendations and/or requirements of your local home energy audit program or building code. For example, some areas of your home may need higher R-values than others due to varying climate conditions or the materials used in your building.
To determine how much insulation you will need to install, measure the width and height of each wall. Then, divide each length by the number of studs to calculate how much of each wall will need to be covered. If the wall contains openings like doors or windows, you will need to subtract their area from your total wall measurement as well.
If you are insulating an existing house or metal building, the method you will need to use to insulate your walls and ceilings will vary depending on whether the building is still in construction or already completed. When working on an unfinished building, you will have more options to choose from because you can use batt or blanket insulation as well as blown-in products or rigid foam panels.
If you’re insulating an unfinished floor, you will need to remove any furniture in the room and pull up the subfloor. With the help of a stud finder and/or magnet, locate the floor joists and then use a hole saw to cut 4″ holes into the floor (ideally, these will be centered on each joist). Insert the rigid insulation hose and fill each hole until you have full coverage of the joist network. Then, once the hose is removed, place a strip of plywood over each hole cutout and screw it into place.
Materials to Consider
Insulation reduces energy consumption, which saves money on heating and cooling bills. This also helps preserve non-renewable natural resources and cuts greenhouse gas emissions, lowering the risk of global warming or acid rain. High-quality insulation also makes a house more comfortable and easier to maintain, saving homeowners time and money. Insulation and air sealing help maintain healthy indoor temperatures that block out pollutants like pollen, dust mites, volatile chemicals and cigarette smoke that can trigger respiratory illnesses.
There are many types of insulation materials, ranging from bulky fibers to sleek foils. Bulky materials, such as fiberglass, rock wool, and cellulose, trap air or another low-conductivity gas inside their cells to resist conductive heat flow in a building cavity. Rigid foam boards, such as expanded and extruded polystyrene (EPS and XPS), resist conductive heat flow through wood framing by preventing the transfer of heat between the outside of the wall or roof and the inside.
Rolled insulation, made of fiberglass, cotton, mineral wool, and plastic fibers rolled into sheets, is one of the most popular types. It is affordable, easy to install, and can be cut to fit around rafters, walls, and floor joists. It’s available with or without a facing, which helps facilitate fastening during installation and acts as a vapor barrier or air barrier. All rolled insulation should be installed with a vapor retarder to prevent condensation that can rob insulation of its R-value and encourage mold growth.
Foam board or rigid insulation is an excellent choice if you’re building a new house or adding insulation to a current home. Foam insulation can be fabricated into ducts at the factory or, in some cases, by HVAC contractors at the job site. It can also be applied as liquid sprayed insulation or as laminated foam panels with a variety of facings. Foam insulation manufactured today uses a non-HCFC (hydrochlorofluorocarbon) foaming agent.
If you’re planning a new construction, consider structural insulated panels (SIPs) or insulating concrete forms (ICFs). These products include insulation built into the form of the house, reducing thermal bridging and maximizing wall R-value. In addition, advanced wall framing techniques can improve the overall R-value of a traditional framed house by minimizing voids between wood studs.